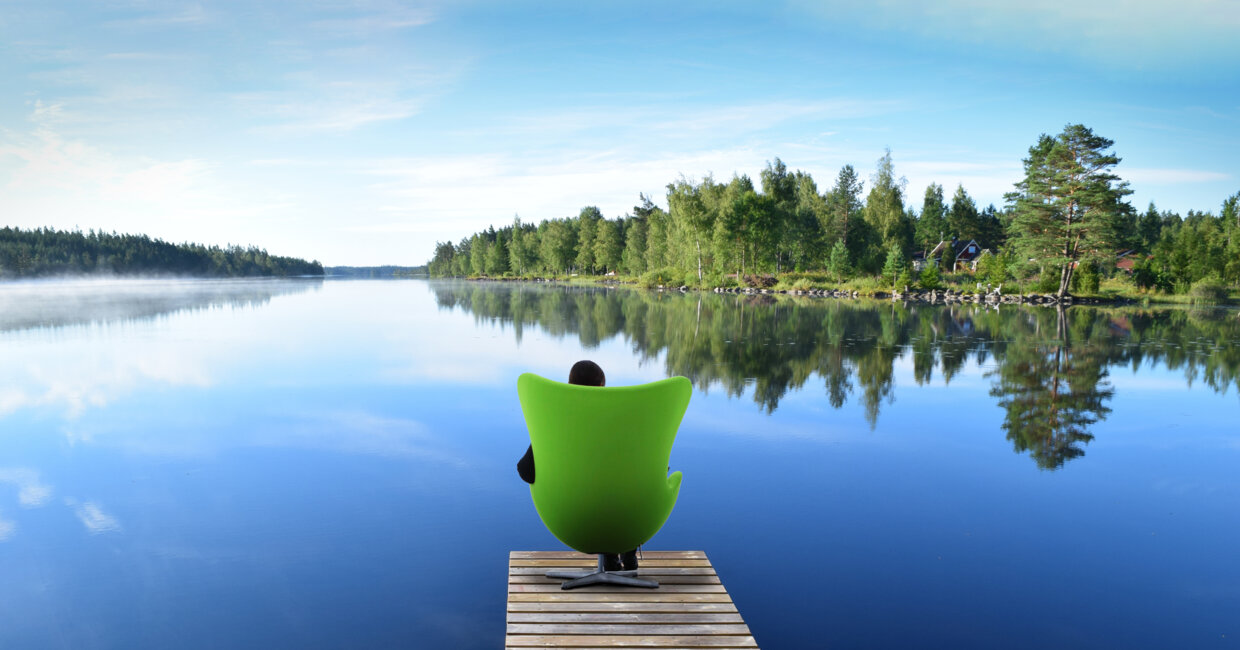
Five steps towards sustainable cargo handling
Kalmar is helping terminal and logistics operators lay the foundations for a more sustainable future through a step-by-step approach addressing the challenges arising from the transition to eco-efficient cargo handling.
Public pressure, increasingly strict legislation, investor demands and local requirements are just some of the factors behind the drive for sustainable terminal operations.
As a result, ports have become actively involved in efforts to cooperate on environmental protection and sustainable development - according to the European Sea Ports Organisation, 96% have an environmental policy in place.
Cargotec has committed to reducing its CO2e emissions and those of its suppliers and customers by one million tonnes by 2024 and reducing CO2e emissions in Kalmar Mobile Solutions only by 550,000 tonnes.
Kalmar has identified five key steps for terminal and logistics operators to achieve sustainability objectives as outlined below.
Develop an ‘eco vision’ and target
“Companies have to be transparent about their sustainability goals and understand what they mean for a specific site or terminal,” says Lasse Eriksson, Vice President of Technology at Kalmar. “They have to take account of the legislation and regulation that affects their business, and recognise that all stakeholders need to reach their own sustainability goals.”
The first step is to determine the target state, which could be described in terms of targeted reduction of CO2 emissions and the timeline for getting there. Once this is determined, it is necessary to identify the baseline by evaluating emission levels in the current operations.
This baseline and the future vision will then be used as a foundation for the roadmap that will define the actions needed to get from the current state to the future target.
The data generated by fleet management tools such as Kalmar Insight is invaluable in establishing this baseline.
Create an infrastructure strategy
One of the major challenges for creating eco-efficient cargo operations is accessing a sustainable energy supply.
An example of a sustainable electric energy value chain is where additional renewable energy is produced using solar panels at the port or terminal site station transformer. Should production exceed consumption during sunlight hours, battery energy storage power packs can be charged - to be used when no green electricity is available or during peak consumption hours when electricity is the most expensive.
The available sustainable energy goes into the local power grid from which the operational cargo handling equipment - here with Li-Ion batteries - is charged.
“In addition to sustainability and availability, terminal operators also need to consider manageability and safety – for example, are there any local restrictions on handling alternative energy sources, will the fuelling stations be further away from operations, and what about high voltage safety requirements for electrical equipment,” says Kalmar Counterbalanced Container Handlers Product Portfolio Manager, Mette Kjems Bærentzen.
Then there is the cost of the infrastructure and energy. If price levels cannot be guaranteed, the operator loses control of their operating costs.
Identify solutions that are available and will be available in the near term
Bærentzen notes that cargo handling equipment accounts for around a quarter of total port emissions, although reachstackers and empty container handlers are becoming increasingly eco-efficient without compromising productivity and efficiency.
Customers often ask if electrification will impact productivity because of the need to charge electric equipment more often than they would refuel a diesel machine.
But if we look at productivity time versus idling time for diesel reachstackers, the average idling time is 30% with almost half of all running hours being used for 25%-45% idling. If even half this time was used to drive to a charger, plug in the machine, charge and resume handling, the potential savings would be considerable.
Innovations in this area include:
- Eco-efficient powertrains - finding the most energy efficient solution for cargo handling equipment using either batteries or hydrogen fuel cells
- Productivity adapted energy consumption - using different energy availability settings according to required performance
- Lightweight design using high strength materials - making heavy equipment lighter, which requires less energy to move around and reduces wear and tear on tyres
- Optimising energy accumulation - what goes up must come down, so harnessing energy from the power of gravity will reduce external energy requirements
Battery management is also crucial. Incorrect charging patterns can damage batteries and reduce their lifespan, so appropriate training should be provided to help customers and users maintain batteries in good condition as they are, in the end, one of the most expensive components on the machine.
Kalmar has committed to having an electrically powered version of every machine in its range by the end of this year.
Understand the business case and future operational scenarios
“When defining actions and building the business case, you need to understand your future operational scenario,” says Eriksson. “You might have good business projections and strategies already in place, but there are also many general indicators that could be used as a point of reference to understand the volume of future operations. Then you would need to map the future scenario to tangible operational parameters, such as how many moves you will be doing, the weight of loads moved, and distances driven.”
The final stage is about making the most of eco-efficiency investment. Drivers and technicians need to be prepared for a new type of operation and terminal operators can use the real time data from their operations to monitor machine performance to ensure targets are being met.
Consider implementation and how to get the best out of eco efficient projects
Return on investment should be based on total cost of ownership calculations. Electric equipment will have fewer moving parts, longer maintenance cycles and therefore could cost 50% less to service and maintain. In addition, they offer more predictable operating costs as the price of electricity is more stable than that of diesel fuel.
Customers can also avail of the Kalmar fuel saving guarantee. Available with all electrically powered Kalmar forklifts and Eco reachstackers, this guarantees a fixed energy/fuel consumption per hour and compensates the user if the guaranteed consumption is exceeded, limiting the risk of variable cost overrun.
Driver and technician training plays a vital role in ensuring customers realise the full benefits of eco-efficient solutions. Safety training should be highlighted in the context of new electric solutions, while the optimal use of new driveline technologies may differ from the previous ones. For terminal operators, switching to electrically powered equipment will have a fundamental impact in terms of infrastructure, workflows, maintenance, people and skills. It is therefore essential that operational data is turned into usable intelligence and shared across all stakeholders.
Sustainability is ‘today’s opportunity but tomorrow’s liability’, so a methodical approach to addressing the challenges faced by terminal and logistics operators is crucial.
Lasse Eriksson and Mette Kjems Bærentzen shared their insights and recommendations on how to start the journey towards a fossil-free future during a webinar hosted by Kalmar in May – a recording of the webinar is available at https://www.kalmarglobal.com/news--insights/webinars/towards-eco-efficient-cargo-handling-operations/
Related articles
Further reading
Subscribe and receive updates in your email
Abonner på våre utgivelser